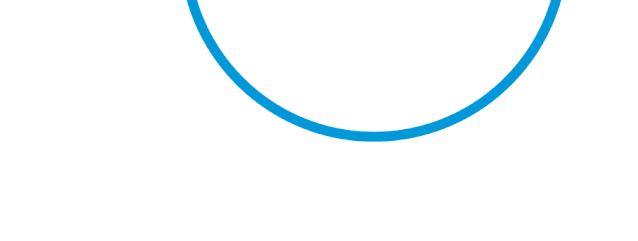
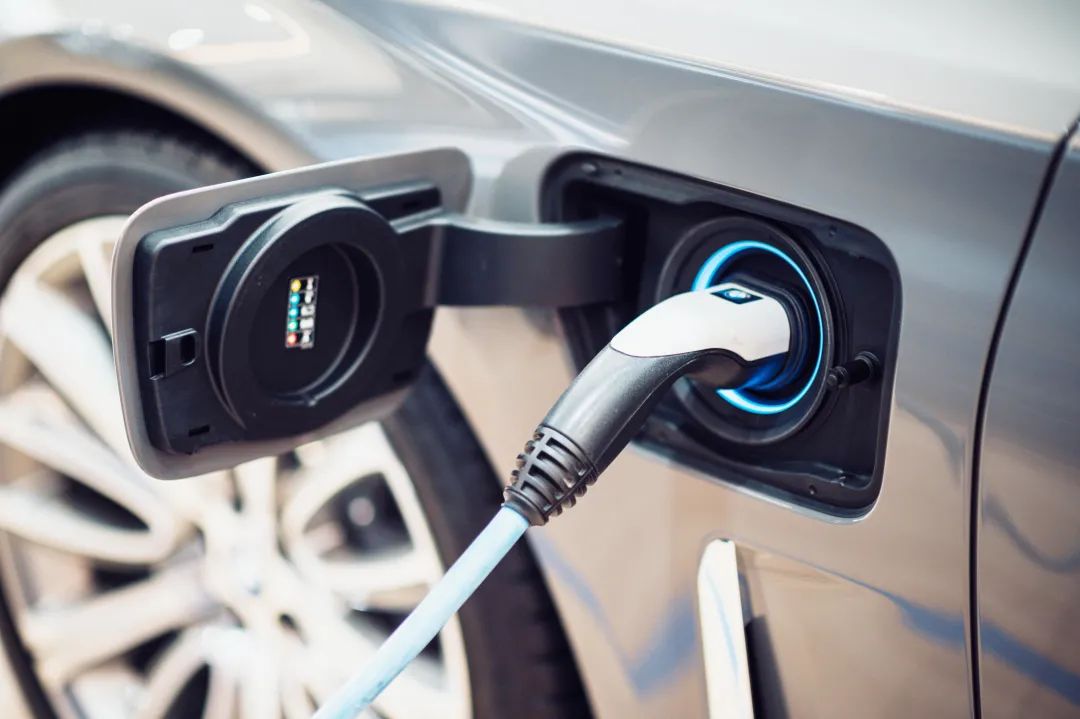
近年来,新能源电动汽车一直备受关注,也是越来越多家庭买车的首选。但续航里程短、充电时间长始终是无法绕开的问题。怎样才能跑得更远?创新技术和材料的应用正为电动汽车发展注入了强大的助推力。
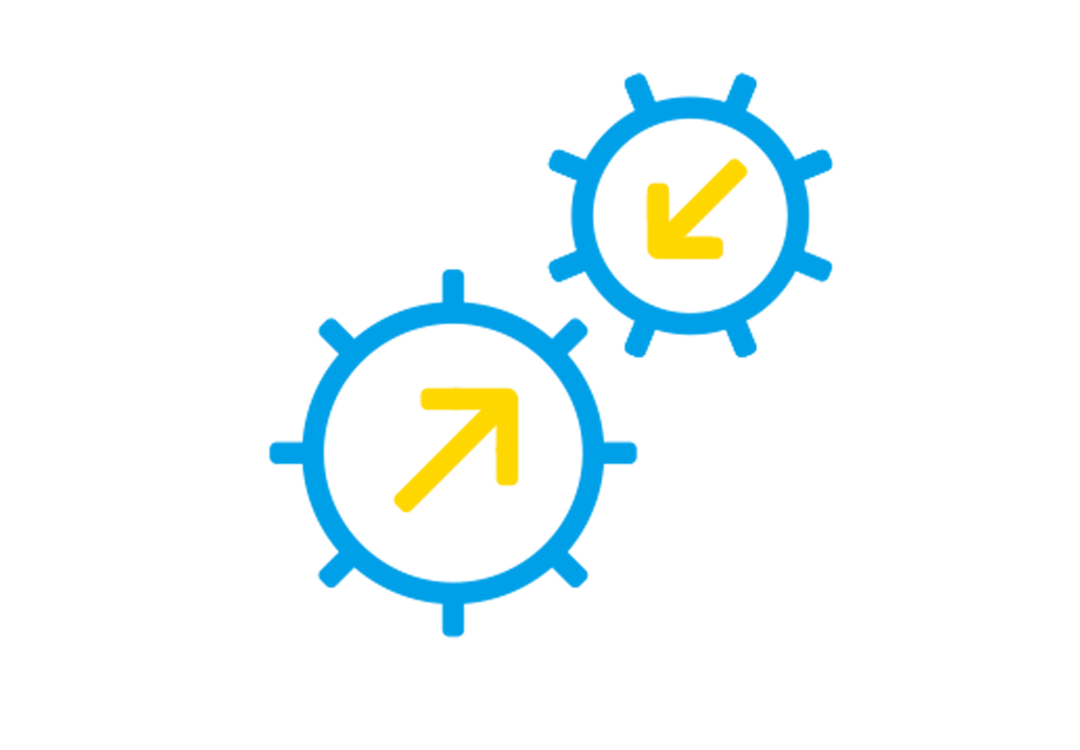
内“心”强大,当然跑得远
电动汽车能跑多远、多久,与2个关键点密不可分。一是核心部件电池组的容量,二是电动汽车自重以及承载的重量。

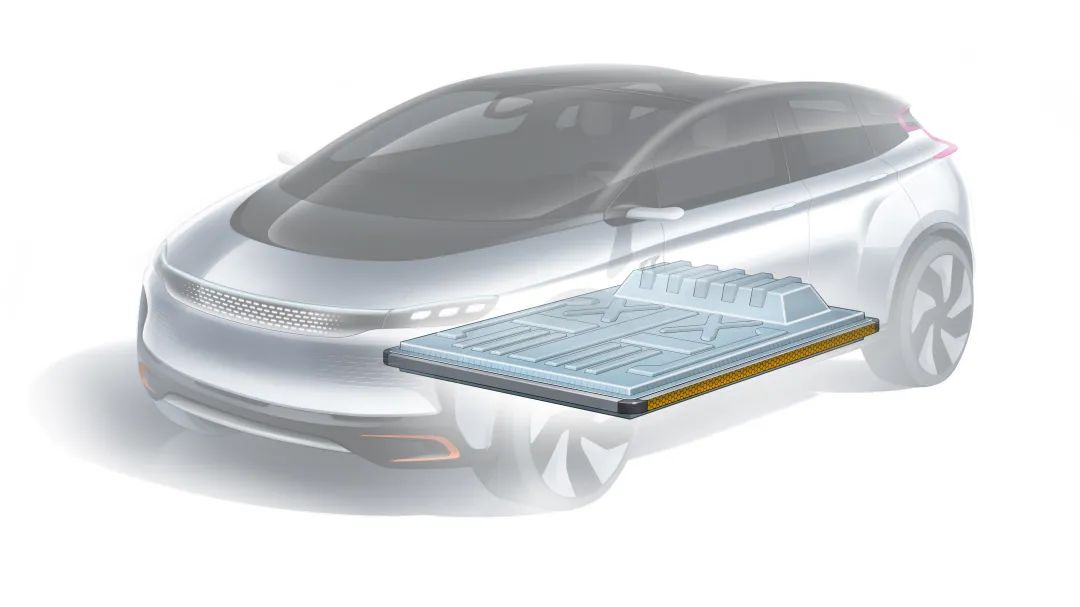

电动汽车电池组
我们知道电动汽车靠电力运行,动力驱动需要通过一个或多个电池组供电来完成。随着续航需求的提升,电池组数量在不断加大,这使得整个电池系统的体积变得越来越大,也越来越重。这能量和重量间不可调和的矛盾,直接阻碍着续航瓶颈的突破。
SABIC 的汽车团队带来的轻量化热塑性材料的电池组设计方案,就能轻松应对这些挑战。
电池外壳和结构组件选用SABIC热塑性材料来替代金属材质,电池组系统中单个组件的重量可减轻 30% 到 50%。重量减轻了模块中的电池更容易堆叠组合,更可提升高达15%的能量密度。所采用的阻燃 (FR) 树脂材料还有效地降低了电池长时间使用发热带来的风险。
现在SABIC创新电池组设计方案正在电动汽车各种电池组应用中大显身手,带来强劲稳定的能量支持,让你彻底摆脱“在充电桩方圆百里转圈圈”的尴尬。
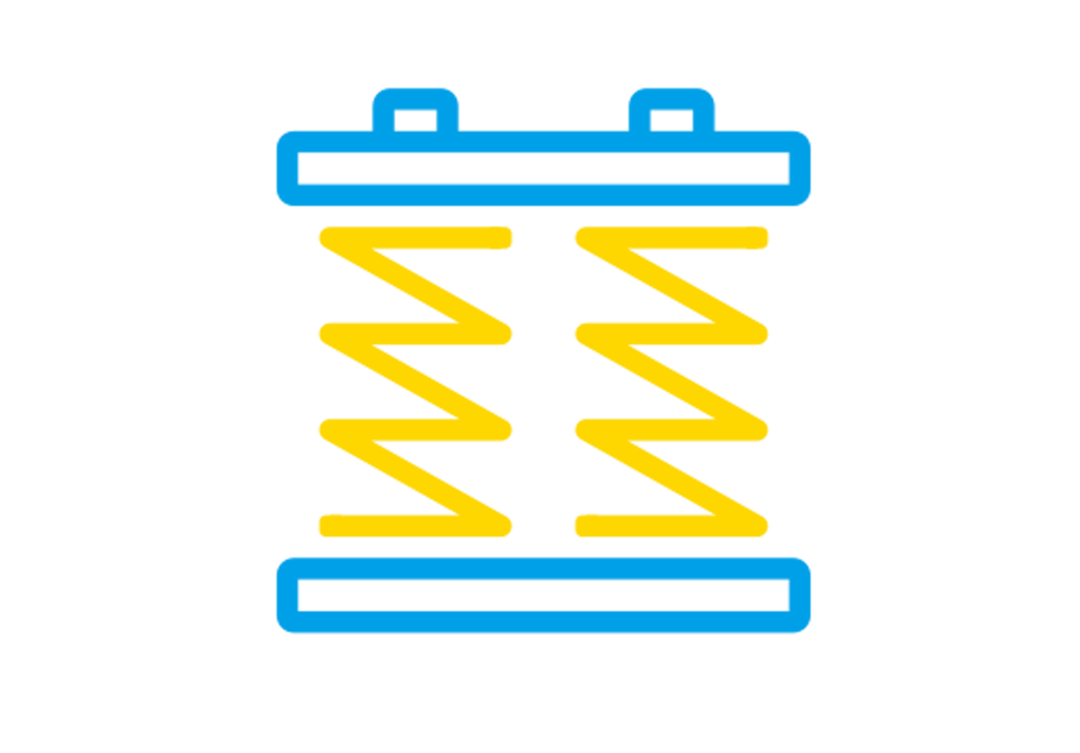
无惧碰撞,给“心”最好的保护
想要电池组这颗“心脏”健康正常运作,发挥最大的能量,悉心保护少不了。
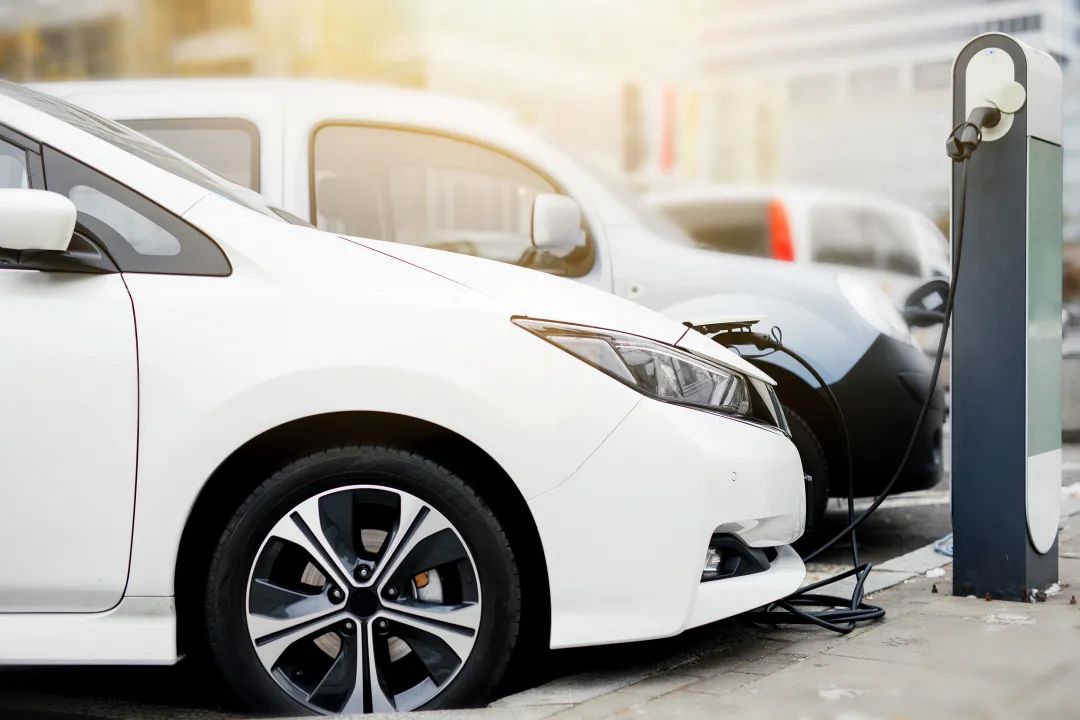
中国最近出台了电动汽车安全新标准。这些标准已于 2021 年 1 月 1 日起生效,强调应在电池系统安全方面实施包括碰撞保护在内的多项改进。
电池组通常被安装在电动汽车底盘上,虽说是完全封装的结构,但遇到碰撞,对电池组也会产生不小的冲击力,进而引发部件损坏不能工作。常规的方法是用钢片、铝材加固件来应对,但同样是面临增加车辆重量的问题。
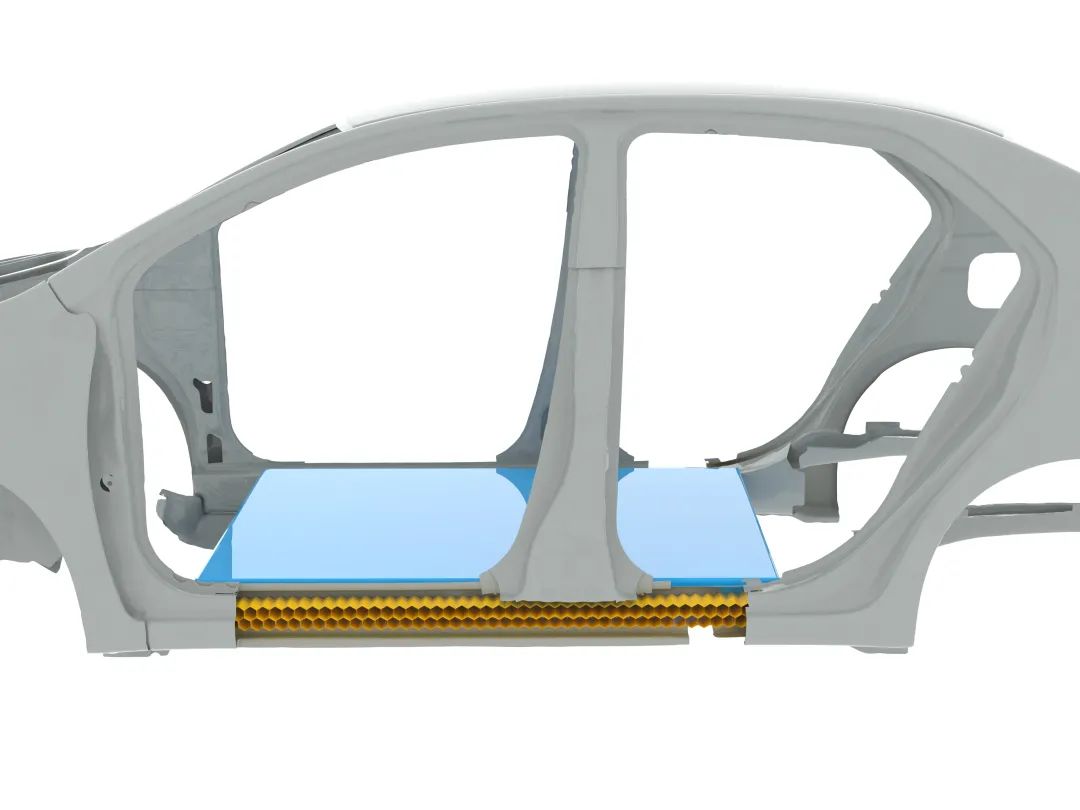
电池组封装结构及安装位置
现在还是把难题交给SABIC汽车团队。SABIC专家们将采用结构混合替代方案来解决,选用SABIC聚酯合金材料——XENOY™ HTX 树脂,替代单一的金属材质,制造出的防碰撞组件质地轻巧,又能有效吸收冲击力。
在发生碰撞时可自行承受变形压力,最大限度减少了对电池组的损坏。这看似简单的材料替换方案,却是SABIC数十年来在碰撞和安全应用材料解决方案领域专业知识的积累和转化。
看到这里,你是否对这场电动汽车续航力的battle充满信心?
SABIC 的团队凭借专业和创新的技术,不仅可以在材料选择方面提供建议,还可以提供工程资源,为车辆电池组设计的开发和优化提供支持,为电动汽车的快速健康的发展出力。